Introduction
When working with electrical systems, understanding how input devices function is important to ensure smooth operation. A key aspect professionals must determine is whether a system uses wet or dry contacts. These two methods have distinct functions, and choosing the better option depends on the specific device and power supply involved.
A wet contact means the terminal is directly energized when the relay or switches close, allowing voltage to pass through without needing a separate power source. In contrast, a dry contact requires an isolated supply, making it more versatile in industrial settings. The difference lies in how the circuit is completed, which affects how troubleshooting is performed. Looking at an example, engineers often rely on wires and diagram analysis to trace output signals. When working with relays, knowing the standards for contacting is one of the most common challenges.
From my experience, understanding this concept makes it easier to measure performance and drive efficiency in control systems. Whether working with brands of devices in varying models, knowing how each moment of activation impacts the load is crucial. I once faced an issue where the job involved tracing a faulty triangle of connections between multiple sensors—a challenge that could have been avoided with a clear diagram. The key takeaway is that knowing why and when to use a dry or wet contact can make all the difference in electrical system reliability.
What is a dry contact?
A dry contact is a type of switch that does not have voltage directly supplied to it. Instead, it relies on another source to provide power, making it a passive component in a circuit. This design is commonly used in relay systems, where the primary contact controls the flow of electricity without directly affecting the secondary sets of connections.
From my experience, I have seen dry contacts effectively monitor critical alarm setups, such as fire and burglar alerts in security systems. They also play a role in AC distribution, ensuring isolation between circuits. These functions allow for a complete separation between the controlling and controlled circuits, reducing risks. In many figures of electrical design, a dry contact will break or make a connection without interfering with the main power path.
For safety, these are often used in applications where the voltage is less than 50 volts, ensuring no unnecessary exposure to high electrical energy. Dry contacts are an essential component in automation and industrial control, providing a standard method to maintain connectivity across different systems.
Key Differences Between Dry and Wet Contacts
When working with relay-based systems, understanding how switching works is crucial. A dry contact does not have voltage supplied to it internally, meaning the power must come from an external source. These contacts operate like a simple switch, where the circuit is either open or closed based on an external action, such as pressing a button. The concept also applies to discrete devices, where no direct electrical connection is made within the switch itself. In contrast, a wet contact has power already present, so when the switch is turned on, the same supply is sent to the load.
From my experience, working with PLC systems has shown me that dry contacts are commonly labeled with COM, IN, and other terminology to help engineers properly wire them. This ensures that the load and contacts remain isolated, reducing interference. In solid-state circuits, optical or transistor-based sensors also use proximity detection to trigger a response.
Unlike wet contacts, which allow power to flow immediately, dry contacts require a separate potential difference to complete the circuit. The discussion around choosing between these two often depends on the state of the system, the group of devices being controlled, and the level of electricity involved. Whether using normal switching methods or more advanced models, knowing the position and function of these components helps in designing reliable control systems.
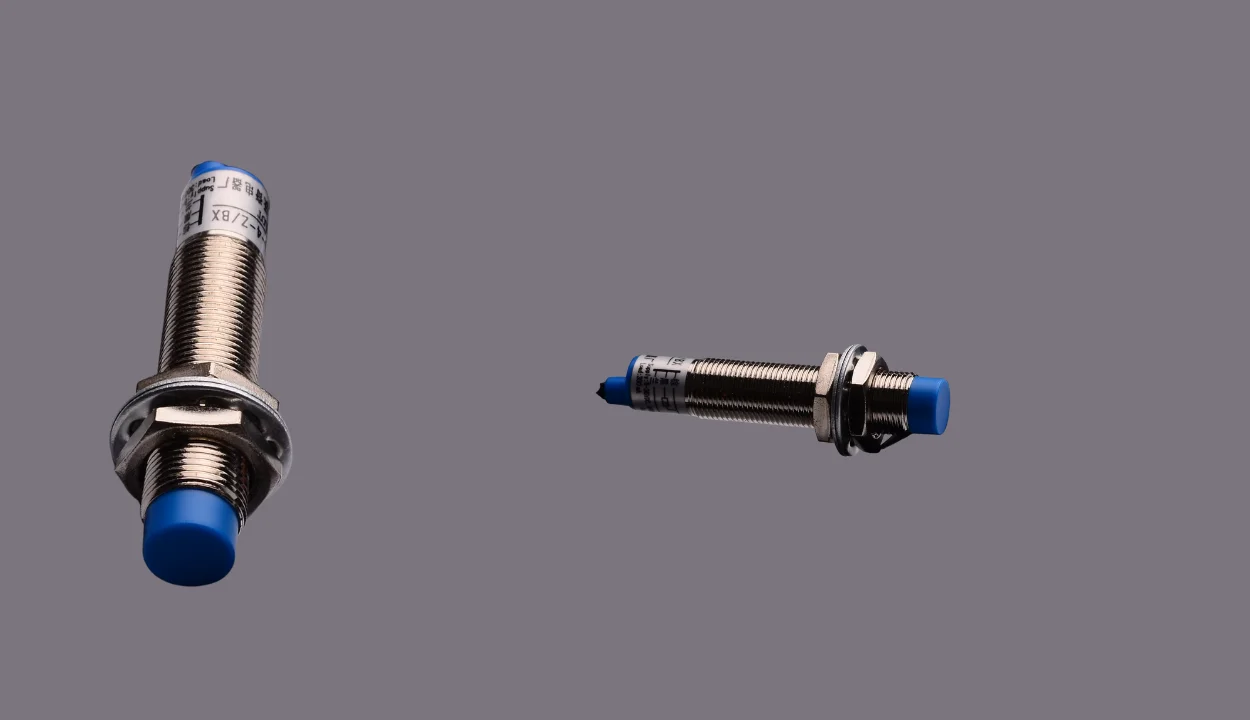
Practical Uses of Dry and Wet Contacts
In many electrical systems, relays are a common method to control circuits, especially when isolation or voltage conversion is needed. A dry contact is often seen in ground fault interrupter (GFI) circuits, where the same input wires both provide and remove power from the system. These circuits are designed to handle thousands of volts, offering superior protection by ensuring the circuit remains isolated from direct power sources. In larger control setups, optoisolators are also used to withstand sudden surge currents, preventing damage to sensitive devices. One example is industrial PLCs, where different voltage levels are used for switching operations, ensuring efficient transmission of signals while maintaining circuitry safety.
On the other hand, wet contacts simplify wiring, making them ideal for small-signal applications like sensors that interact with automation systems. These contacts ensure continuous power flow without needing an extra relay or switching unit. In some cases, where the power consumption is minimal, such as in security or alarm systems, a wet contact setup ensures seamless output transmission.
Load control applications, including motor starters, benefit from the immediate power supply that wet contacts provide. For industrial safety, breaker circuits incorporate these contacts to quickly interrupt power downstream, preventing electrical failures. When properly designed, both dry and wet contacts serve distinct roles, ensuring efficient electrical construction while improving system advantages.
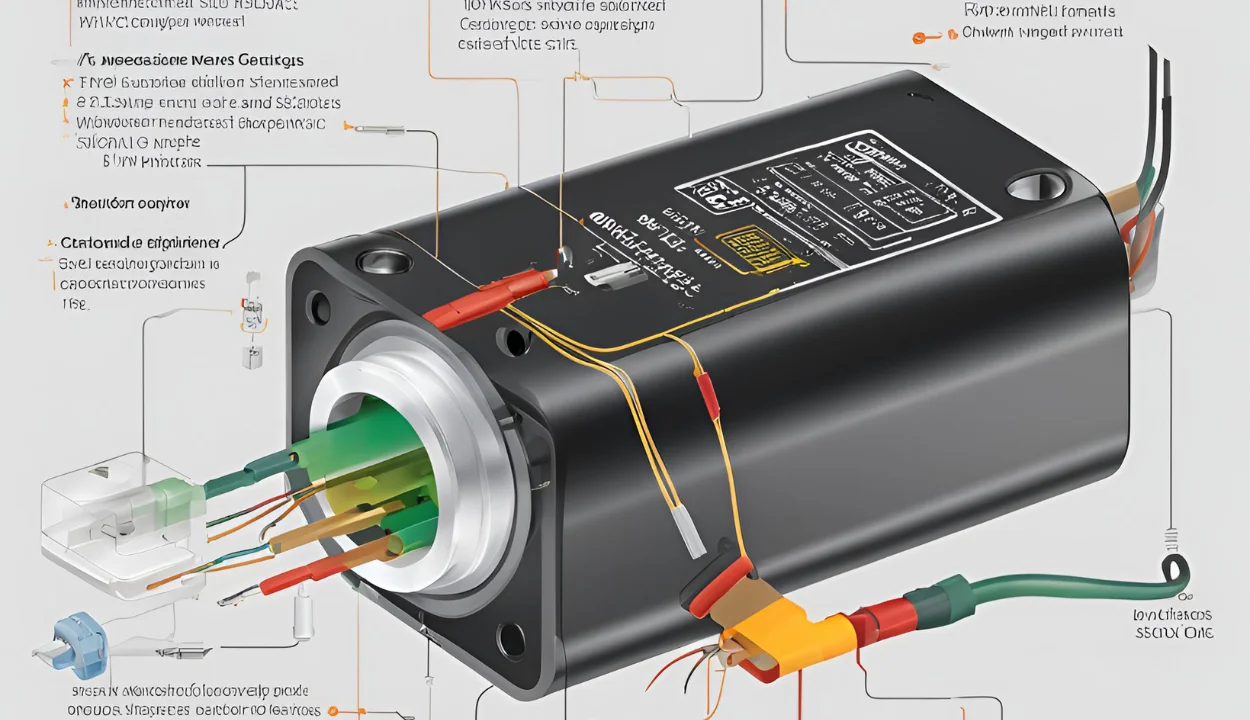
How to Identify Contact Types
A simple way to begin identifying whether a contact is dry or wet is by checking the number of wires connected to the device. In most cases, a wet contact has an internal supply that sends power directly to the load when activated. This is common in relays, where the same voltage is applied to both the input and output.
On the other hand, a dry contact requires an external power source, meaning the switching action is fully performed by the relay or control circuitry. A common example is in modules used in automation systems, where the input signal triggers a separate power path. Be careful, though—some devices may have additional terminals for open or closed states, but this does not always mean they function as a dry contact.
Another key factor is how the switching is driven. In programmable logic controllers (PLCs), the processor sends a low voltage signal, often 5V, to trigger an external relay. Unlike wet contacts, where power flows immediately, dry contacts need an action from the control system before transmitting power. Digital sensors also use variable frequency signals to drive responses, making them different from common relays.
Some restricted types of control circuits only function with a specific AC or DC power range, and in rare cases, they may have extra components like optoisolators for additional protection. A larger industrial system may include multiple drives or terminals to handle different circuit setups, further emphasizing the importance of correctly distinguishing between dry and wet contacts.
Conclusion
Choosing between dry and wet contacts depends on the application and system needs. Dry contacts offer isolation and a wide variety of voltage options, making them ideal for devices that need flexibility in switching and control. On the other hand, wet contacts are automatically given power, ensuring simplicity in wiring and consistency in levels, which makes troubleshooting much easier. If the main focus is control and safety, dry contacts are preferable, while for seamless operation, wet contacts provide key advantages in certain systems. Understanding these differences helps in making the right choice based on the power needs of the application.