Introduction
When I first came across capacitive technology, I was amazed by how effortlessly it detects nearby objects without direct contact. This technology operates using an electric field, making it incredibly useful in various applications. A detailed understanding of its working of capacitive sensor shows that as an object enters its proximity, it alters the field, allowing the sensor to react. Over the years, I’ve explored different types of these sensors, each designed for specific tasks. Whether used in touchscreens or industrial automation, their effect on modern technology is undeniable. This comprehensive guide offers a fresh look at how capacitive sensing shapes the way we interact with devices.
What is a capacitive sensor?
A capacitive sensor is a smart device that can detect both solid and liquid targets without direct contact. It works by emitting an electrical field from its sensing end, and when an object enters, it disrupts the field, allowing the sensor to respond. These sensors are widely used for precise detection in industries where physical touch is not ideal.
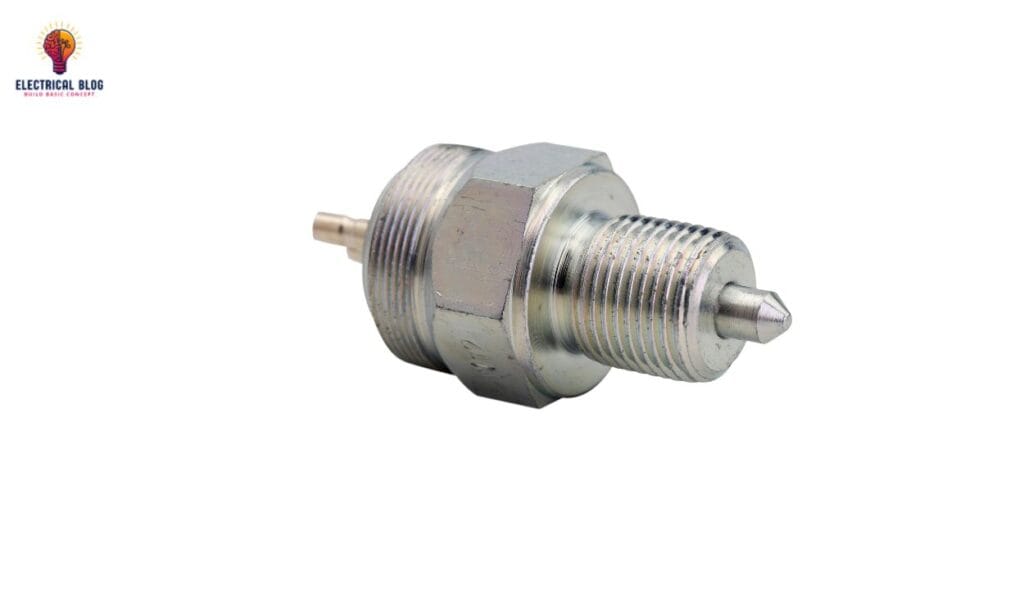
Working of a capacitive sensor
A capacitive sensor operates by generating an electrostatic field between its plate and the target, forming capacitance that changes when an object enters the sensing face. This change is processed through an oscillation-based circuit, which increases until it reaches a threshold level, causing the sensor to be activated. Unlike an inductive sensor that relies on an electromagnetic field, a capacitive sensor can detect both conductive and non-conductive materials, making it versatile.
The sensitivity of the sensor can be adjusted using a potentiometer, an integral touch pushbutton, or even remotely through a wired connection. If fine adjustment is not available, the sensor may need to be physically moved for accurate detection. Increasing sensitivity extends the operating distance, but excessive adjustment can make it influenced by temperature, humidity, or even dirt, affecting performance. Proper calibration ensures reliable output in different conditions.
Conductive and non-conductive targets
A capacitive sensor can detect both conductive and non-conductive targets, making it useful in many industries. Conductive materials like metal, water, blood, acids, bases, and salt have higher capacitance, which does not require reduction factors to adjust the sensing distance. However, non-conductive materials act as insulators and depend on their dielectric constant, a value used to measure how materials like wood, grain, paper, and dirt affect detection.
Since air and vacuum have very low capacitance, materials with a greater content of moisture or density will result in a longer proximity range. In contrast to inductive sensors, which rely on electromagnetic properties, capacitive sensors work with a variety of categories of materials, regardless of their metal strength.
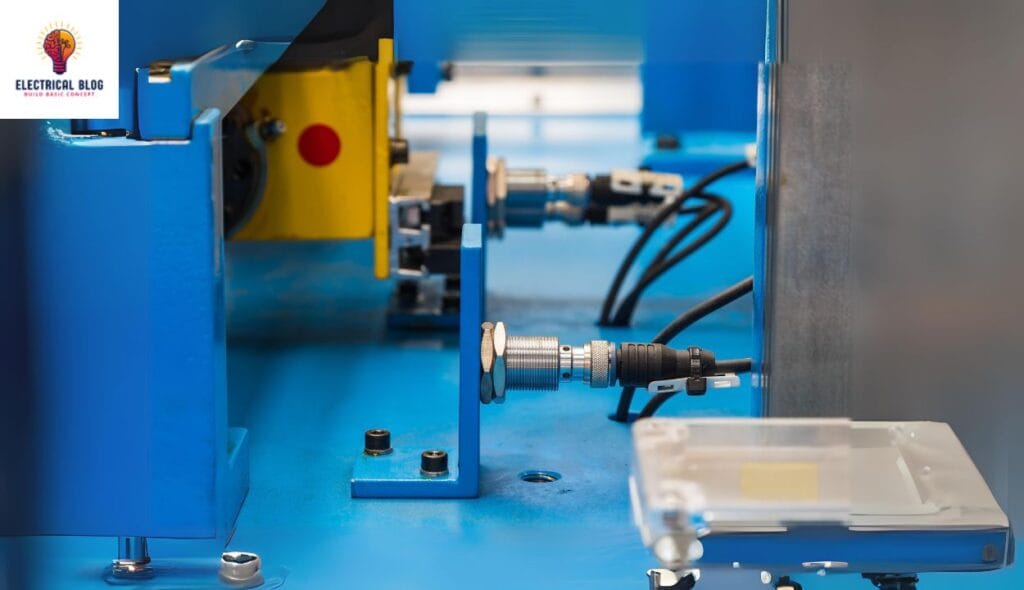
Key Elements in Sensing Distance
The sensing distance of a capacitive sensor depends on three factors. First, the size of the active surface—a larger face results in a longer range. Second, the dielectric constant of the material, which is referred to as how well an object holds an electric charge—a higher constant improves detection. Third, the area of non-conductive targets, where a bigger surface allows for better detection. External conditions like temperature and speed have a minimal effect but can still determine performance in certain applications.
Understanding Sensing Range
The sensing range of a capacitive sensor depends on multiple factors, including the target material, size, and environmental conditions. The standard way to measure this range is using a Fe 360 plate that is 1 mm thick, with its length equal to either the diameter of the registered circle or three times the rated sensing distance, whichever is greater. Non-metallic objects require a reduction in the sensing range based on their dielectric constant, and this adjustment must be measured carefully. Some manufacturers provide an approximation of this reduction in their catalog, but real-world performance may differ due to operating temperatures and voltages.
To ensure effective sensing, the nominal range Sn and effective range Sr must be considered. The actual sensing range can be fine-tuned using a potentiometer, pushbutton, or remote wire. If no electronic adjustment is available, the sensor’s mounting position may need to be adjusted physically. External influences like Ta +/- 5°C and flush installation can also impact performance. Sensors operating at different voltages and supply conditions should be tested under specified conditions for accuracy, as tolerances in marketing materials might not always match real-world use.
Understanding Hysteresis
Hysteresis is the small difference in sensing distance between switch-on and switch-off when a target approaches and then moves away from the sensing face. This is designed to prevent chatter in the output, ensuring stable performance. The stated value of hysteresis is often given as a percentage (%), such as 15% of a rated 20mm range, meaning a 3mm shift. Various factors like temperature, humidity, pressure, and mechanical stresses on the housing can influence it. Since it is correlated to sensitivity, a larger sensing range often results in higher hysteresis. Internal electronic components, including printed circuit board elements, are also utilized to manage this independent parameter.
Measuring a sensor’s sensitivity
To determine the sensitivity of a capacitive sensor, a target is moved towards the sensing face until the output is activated. The distance at this point is carefully measured using a micrometer while ensuring the plate is grounded to the negative power supply. The target is then moved back to note when the output turns off, which helps identify the hysteresis range.
A potentiometer is often used to set the sensor’s sensitivity, but it does not always provide an accurate indicator due to linearity inconsistencies. Many potentiometers lack hard stops, instead using clutches to prevent them from getting damaged when reaching the maximum or minimum adjustment. Since the application may require precise control, the number of turns must be carefully observed to maintain a consistent setting.
Practical Applications of Capacitive Sensors
Capacitive sensors are widely used in workstations, robots, and conveyors for detection and counting tasks. They can trigger a signal to detect a part on an assembly line or activate a counter to track how many items are built. These applications also include checking fluid levels in a tank, where they help monitor high or low liquid levels and send alarms when needed.
Conclusion
Capacitive sensors play a crucial role in modern automation by offering reliable detection, counting, and checking capabilities across various applications. Whether used in workstations, conveyors, or robots, they provide precise signal activation and trigger mechanisms to streamline operations. Their ability to monitor fluid levels in a tank, ensuring that high or low thresholds are met, adds to their versatility. With advancements in capacitive technology, these sensors continue to enhance efficiency and accuracy in industrial and commercial settings.
Read more: